Factories struggle to keep skilled workers
Hong Kong businessman Ronnie Cheung squirms as he watches an army of migrant workers queuing in front of Shenzhen's train station, waiting to buy tickets home for the Lunar New Year.
'I wonder if any of my workers are there. I just hope I will get all of them back when the holiday is over,' said Mr Cheung, owner of a Shenzhen jewellery workshop.
Factory managers across the Pearl River Delta share the same concerns around this time every year as hundreds of thousands of migrant workers pack up and head home. When the Lunar New Year holiday is over, 10 to 20 per cent of them - usually the most experienced and skilled employees - will probably not reappear.
The delta has been plagued by a labour shortage in recent years, despite repeated promises by the government that it will solve the problem. Various studies estimate there will be a shortfall of between 2 million to 2.5 million workers in the delta this year.
'This year there will be about 3.4 million new jobs created in Guangdong, but our local schools can supply only 1.4 million new labourers,' said Lu Zhiguo , an economics professor in Shenzhen who specialises in labour issues. 'Two kinds of workers will be particularly hard to find: skilled ones and those who have to perform dangerous or dirty duties.'
According to a study by Professor Lu, there will be 3.2 job vacancies for every skilled technician or worker with specialised skills in the delta this year. Many factories are struggling to retain experienced staff and fighting hard in the market to recruit new ones.
Gary Lo, chairman of the Federation of International Small and Medium Enterprises in Hong Kong, said: 'The problem is getting worse. The situation is particularly bad in the textile industry. Some factories are 30 per cent or even 40 per cent understaffed. Many orders cannot be delivered in time as a result.'
Many people are blaming the problem on slow salary growth in the region. While Guangdong's economy has expanded at an average 15 per cent a year during the past decade, salary growth has stagnated for years. Abusive treatment of employees and sweatshop working conditions are common, giving the delta a bad name.
'There is no labour shortage in the Pearl River Delta. When [the bosses] say 'labour shortage', they actually mean 'shortage of cheap labour'. I have never heard of any complaints from employers who are willing to pay,' said Huang Zhiming , a social worker who deals with migrants in Shenzhen.
The authorities obviously hold the same view. Over the past two years, Shenzhen has twice raised its minimum wages and promised to review the issue again this year. Guangzhou and Dongguan also followed suit. The move has brought the salary levels in the Pearl River Delta up to par with the Yangtze River Delta - its main competitor for experienced blue-collar workers.
But the pay rises did little to improve the situation, according to factory managers. 'It's not difficult to recruit ordinary workers. What's hard is keeping the experienced ones. Many workers will only stay for a few years - after they finish their training. They will then go back to their home town or find a better-paid job elsewhere,' said Mr Cheung, adding he lost three skilled goldsmiths last year.
Professor Lu said the problem was a structural one and wage issues alone could not explain the full complexity of the issue. 'The overall supply and demand in the job market is well balanced. But there are many structural mismatches because of the economic restructuring in the Pearl River Delta. We actually have a labour surplus in many areas - particularly in jobs that don't require special knowledge or training. The ratio of job vacancies to the number of workers in these areas is 0.78.'
But as factories across the Pearl River Delta are upgrading their manufacturing facilities, managers are increasingly finding they need workers who know how to operate complicated machinery or produce products for high-end markets.
'In the past, most factories in the delta were labour-intensive, small scale and mainly catered to low-end markets. But this has changed. Labour-intensive factories have moved further inland and you have to move up the industrial ladder if you wish to stay,' Mr Cheung said.
He said the minimum wages proposed by the government could only help protect ordinary workers - who were not in short supply.
'I pay my goldsmiths much higher [than the minimum salary level]. I'm still struggling to keep them. The root of the problem is that the mainland government has not provided adequate training for its workforce.'
The increase in the value of the yuan also compounded the problem. Mr Lo said the appreciation of the currency had increased operational costs by 18 per cent on average.
'For small and medium [Hong Kong] enterprises, it has become more difficult to raise salaries, therefore more difficult to retain trained workers. The next two years will be very gloomy for manufacturers in the delta,' he said.
Professor Lu said the long-term solution was to adjust the rigid education system and train more technicians and skilled workers.
'Our training for workers lags behind our economic development. The education system puts too much emphasis on academic achievement and too little on practical vocational training. There is too little investment in this area,' he said.
In the short term, factories in the delta had to learn to respect and value their staff. 'It is not just about salaries. Providing a safe and good working environment is equally important. If we have too many sweatshop reports, that will only scare away the talent.'
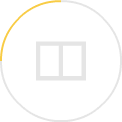